Equipment
-
- Screw Extruder
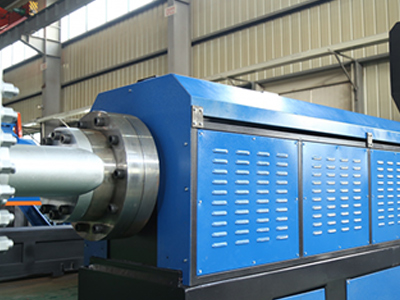
- Two plastic extruder machines are traditionally equipped in a waste plastic recycling line: a main plastic extruder and an auxiliary extruder. The main extruder melts and extrudes plastics, whereas the auxiliary extruder is used to re-extrude materials before pulling the melted plastic into strips and prevent the risk of extruded materials not meeting granulation requirements. The plastic extruder’s screw is made of 38CrMoA1A and has undergone a 72-hour nitriding treatment.
-
- Screen Changer (Melt Filter)
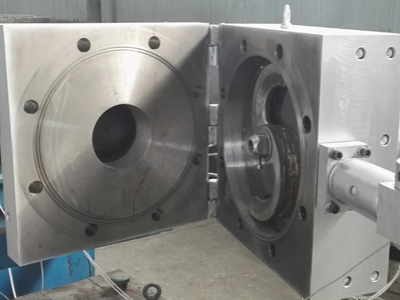
- The plastic extrusion filter system is paired with specific plastic extrusion equipment to filter our extruded materials during the plastic recycling process. This guarantees the quality of all plastic granules produced. We offer hydraulic continuous melt filters and continuous screen changers for customers to choose from.
-
- Cooling Tank
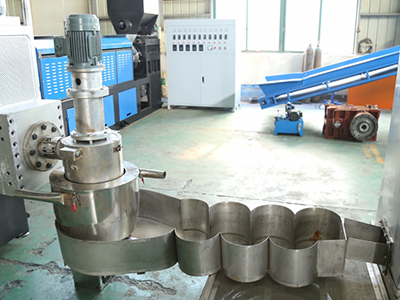
- A plastic extrusion cooler tank is essential to a plastic extrusion granule line as it plays a key role in the cooling time and temperature control of plastic strands produced in a plastic extrusion plant. The cooler tank is traditionally welded of stainless steel materials, ensuring it is corrosion resistant and durable. The cooler tank’s temperature should be no more than 60℃ and cooling water can be added to control the temperature.
-
- Strand Pelletizer
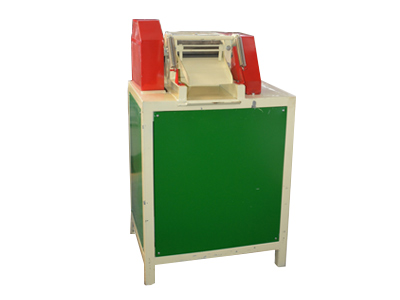
- The silent plastic granule cutter uses 23 rotor cutters to cut granules after the extruding and sand pelletizing processes. It is suitable for cutting PP, PE, PA and other plastics. The granule cutter features a cutting capacity of 300 to 60kg/hour, and its rotor cutters are chain driven for cutting. Compared to a traditional gear drive mode, there is very little wear, the service life has been extended, and features a low noise performance, thus reducing noise pollution.
-
- Conveying Feeders
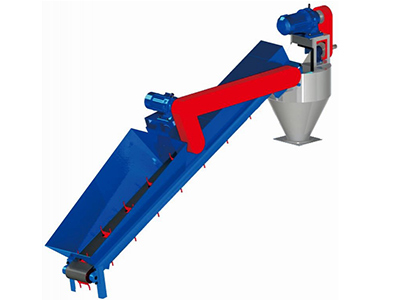
- The plastic recycling smart conveying feeder quantitatively conveys the shredded materials into the main plastic extruder for subsequent plasticizing extrusion. It is equipped with a frequency speed regulation device, allowing users to freely adjust the feeding speed according to the plastic extruder’s extruding speed.
-
- Non-Ferrous Metal Separator
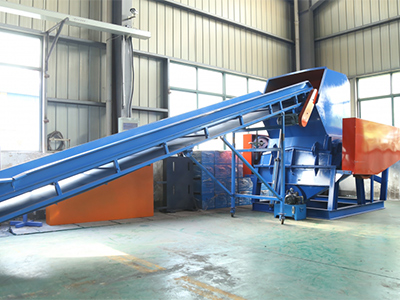
- A waste plastic conveying feeder is used fto convey raw materials to the plastic recycling line. It removes scrap iron in the raw materials with the use of a magnet in the machine and ensures the plastic processing equipment is protected against damages caused by these iron scraps. The magnetic separator can be used in conjunction with a variety of plastic recycling plant equipment.
-
- Vibrating Screening Unit
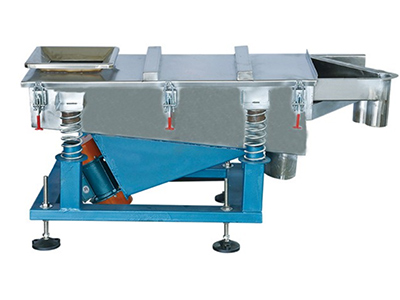
- Plastic plant vibrating screens are used to screen plastic granules during the plastic recycling process. This screen filters out any impurities and powder mixed with the granules to ensure the granules are uniform. This vibrating screen requires an exceptionally lower power consumption of only 250W in its motor. In addition, this screen features a low noise operation, which in turn facilitates a comfortable production environment.
-
- Vertical Silo
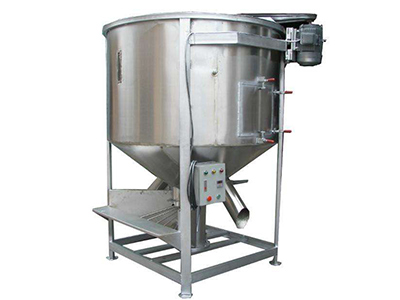
- The plastic plant vertical mixing machine is used to store, mix and dry shredded materials or plastic granules during the plastic recycling process. It mixes materials in a cyclical manner with the use of a screw to ensure an even, uniform mixing performance. The plastic materials are maintained throughout a constant flow condition during the drying process, thus allowing the heat to evenly permeate materials and decrease the drying period.
-
- Storage Silo
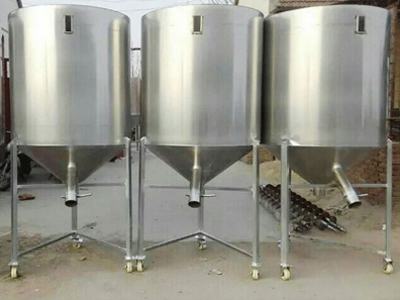
- Plastic storage tanks are intended to store finished plastic granules and are capable of naturally cooling these same plastic granules. When packaging, it pours the granules directly into the bag using a discharge port, which saves employee labor.
-
- Exhaust Gas Cleaning Equipment
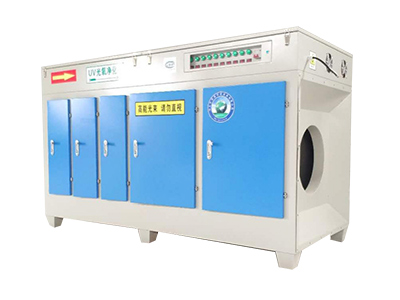
- Exhaust gas cleaning equipment is used to store and handle exhaust gas generated during the plastic recycling process. This equipment will run in a stable, durable manner for 24 hours a day to guarantee the workshop air remains clear and ensures operator safety throughout the surrounding environment. This equipment features a low operation costs and requires no operators for management and maintenance. Simply carry out periodic checking of it to ensure an optimal performance.
-
- Automatic Plastic Cutting Blade Sharper
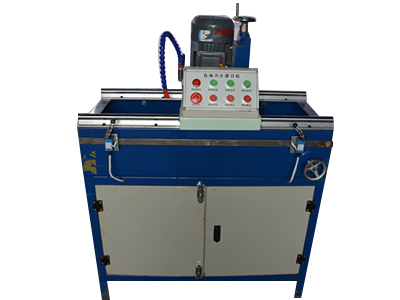
- The automatic plastic cutting blade sharper is used to sharpen the cutting blade of a plastic granulating line. Different plastic processing equipment cutting blades feature different angles, which means that in order to completely sharpen the cutter, this blade needs to feature adjustable angles for sharpening with a grinding wheel. It is ideal for use in a variety of plastic machinery plants and packaging enterprises.
-
- Plastic Bottle Label Remover
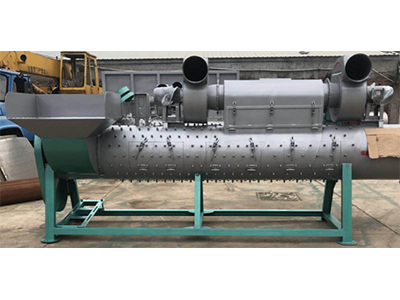
- The plastic bottle label remover is specially designed to remove labels from a plastic bottle and facilitate subsequent processes on the plastic recycling line. The label removal rate is more than 98% during the automatic label removal process, which significantly reduces labor costs and makes it ideal for small to medium sized plastic recycling factories. the label on the plastic bottle, facilitating the subsequent operations in the plastic recycling line.
-
- Electric Induction Heating System
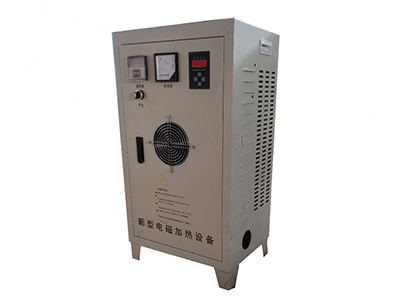
- Electric induction heating systems are designed to heat the machine barrel and other processing equipment parts during the production of plastic recycling granules and perform a better plastic melting process. Compared to a common electric heater band heating device, an electric induction heating system features a faster heating speed, with a temperature rise of 1℃ / second. This saves up to 20% more power and significantly reduces customer production costs.
-
- Electric Control Cabinet
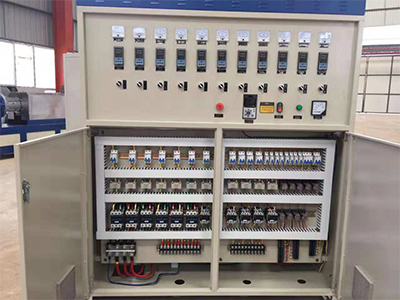
- Plastic plant electric control cabinets act as the “brain” of the plastic recycling line. Users control all equipment operation on the recycling line using switches in the electric control cabinet. It is a complete control system that includes the transducer, AC contactor, switch, PLC, and other equipment. Our electrical engineers can design different control systems for different plastic recycling lines in order to meet a variety of customer requirements.
Our factory has over 30 sets of CNC lathes in the production of plastic processing equipment, such as feeding sawing machine, CNC gantry machining center, CNC screw milling machine, CNC deep-hole boring machine, and cylindrical grinder. Meanwhile, with the adoption of more technologies into plastic recycling, CAD/CAM continues to grow in importance. Thus during the whole manufacturing process, our experienced engineers and technicians utilize CAD/CAM engineering approaches to optimize the entire operation. This allows us to supply high quality plastic machinery with optimal performance.